Grifols Sterile Filling®
Reducing the risk of particle contamination
Technical file
Type of innovation: System
Scope: Bioengineering
Innovation leader: Grifols i Lucas, Víctor
Year: 1989
Period: 1972-2002
Geographical scope: International
Economic impact: Medium
Level of innovation: Disruptive
Patent: Yes
Interdisciplinary connections: -
Ensuring the sterility of plasma products and other medicines that are injected directly into the bloodstream is essential to protect patient health. However, the environment is full of tiny particles that can contaminate intravenous products at every stage of the manufacturing process.
Dealing with an invisible threat
Filling vials and other containers is a crucial stage of the manufacturing process, during which there is a particular risk of particle contamination. The Grifols Sterile Filling® system (GSF®) is designed to reduce this risk by preventing particles from entering the vial during the filling stage.
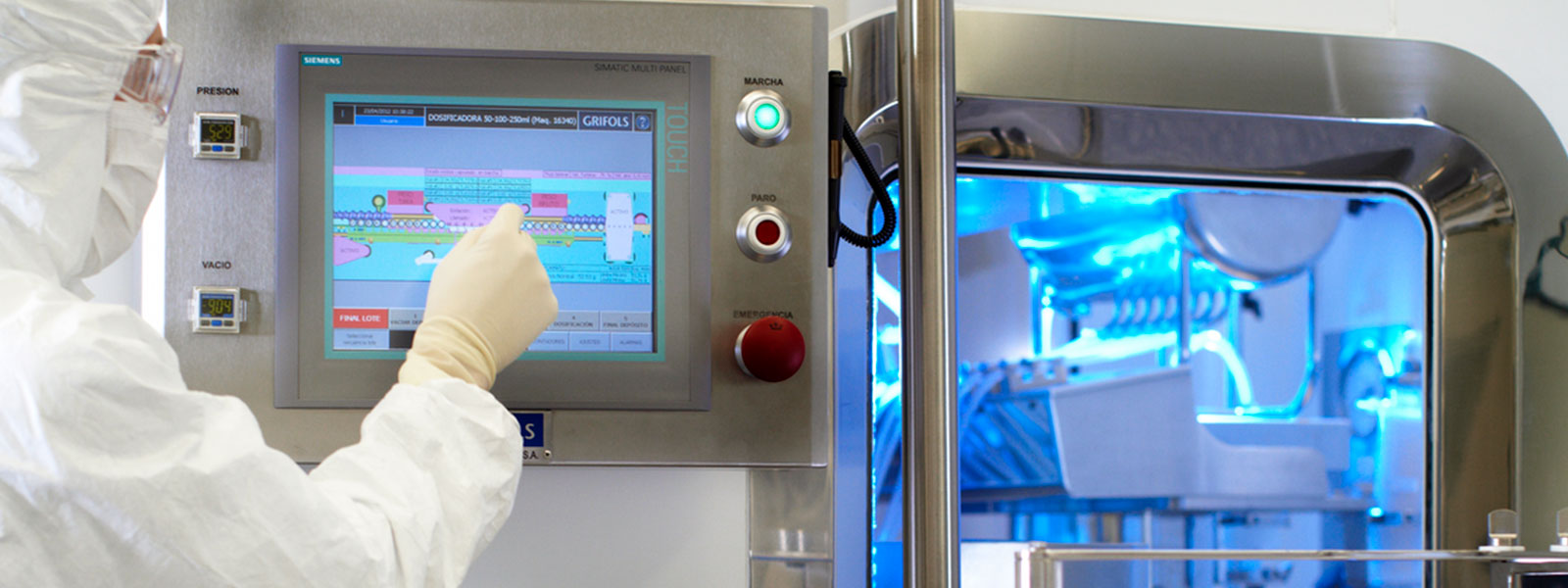
Three key elements
The system consists of three key elements:
- the container
- the rubber stopper
- the protective cap
These elements are pre-assembled and steam-sterilized in an autoclave. Next, the cap and stopper are removed, the container is filled and the stopper reapplied in a sterile environment. Finally, the vials are capped to maintain sterility. The system also monitors the accuracy of the filling machine, using load cells to weigh the vials on entry and exit.
Preventing contamination
Two additional features of the GSF® system are designed to prevent contamination: horizontal laminar air flow keeps the vials free of particles, while the rapid filling process minimizes the time during which the open vials are exposed while being filled.
Membrane filtering technology
The early versions of the GSF® system used a diaphragm pump that had been specifically designed for the purpose by Grifols Engineering and was nicknamed the medusa pump because its shape resembled a jellyfish (medusa in Spanish). Its development was the result of a great deal of hard work, including trials of a plastic triple pump in 1986 and a stainless steel version in 1991, both of which were tested in albumin dosing machines to validate their precision and reliability. Unlike conventional pumps, the membrane did not incorporate valves or moving parts – a major cause of pump malfunction under extreme conditions and also a potential source of particles due to the friction of these components. In later versions of the GSF® system, the membrane was replaced by other technologies.
“Two additional features of the GSF® are designed to prevent contamination: horizontal laminar air flow keeps the vials free of particles, while the rapid filling process minimizes the time during which the open vials are exposed while being filled.”
Bibliography
Grifols i Lucas, V. (2002). Bomba de membrana para líquidos. (Oficina Española de Patentes y Marcas Patente Nº ES2174737). Link.
Grifols, S.A. (2005). Grifols Sterile Filling System: A unique concept for sterile filling processes. [Corporate video]. Barcelona: Grifols, S.A.
Grifols-Lucas, V. (2009). Amb un suro i un cordill. Vivències d'un empresari de postguerra. Barcelona: Grupo Grifols, S.A.
Grifols, S.A. (2011). ¿Y si lo hacemos así? Patentes de Víctor Grífols i Lucas. Barcelona: Grifols, S.A.
Avellà, R., & Miquel, B. (Eds.). (2015). Cuando un sueño se cumple. Crónica ilustrada de 75 años de Grifols. Barcelona: Grupo Grifols, S.A.